Hydrogen in aviation
Member airlines of the International Air Transport Association (IATA) have committed to achieving net-zero carbon emissions from their operations by 2050. Sustainable aviation fuel (SAF) plays the dominant role in achieving this goal, but other less mature technologies are also part of the solution. This article explores the role hydrogen will play in the future of aviation.
Introduction
Hydrogen is the most abundant element in the universe, and, in its liquid form, contains about 2.5 times more energy per kilogram than kerosene, while having the potential to be produced and consumed without creating carbon dioxide. There are two main ways that hydrogen can be used in the place of hydrocarbon based jet fuel: burning hydrogen in a modified gas-turbine (hydrogen combustion) and using engines driven by electricity which is generated via an electrochemical reaction between hydrogen and oxygen (hydrogen fuel cells).
Hydrogen combustion
Using liquid hydrogen as a fuel source is not a new idea; in 1988 an experimental Tupolev Tu-155 flew in the former Soviet Union with one of its engines power by liquid hydrogen. Not only does hydrogen have a higher energy density than conventional kerosene based jet fuel but when burnt, unlike kerosene, hydrogen does not produce CO2 since there is no carbon in the fuel. Instead, burning hydrogen produces water vapour. Hydrogen combustion also produces up to 90% less nitrogen oxides than kerosene and eliminates the formation of particulate matter.
Liquid hydrogen’s thermal-chemical properties are, however, very different from those of kerosene, presenting new challenges for the combustion system within gas turbines. Aside from changing the fuel injection system, the geometry of the combustion chamber needs to be changed to account for the difference in flame speed and temperature when using hydrogen. Beneficially, for the same net thrust the turbine exit temperature of a hydrogen fuelled gas turbine is lower than that of a kerosene fuelled gas turbine, so less turbine cooling is required with hydrogen while also increasing the turbine blade life.
Due to hydrogen’s lower volumetric density, for a given flight length the volume of liquid hydrogen required would be around four times larger than that of kerosene, despite having a lower mass. Hydrogen-fuelled gas turbines therefore only start to become economically viable on larger aircraft, such as mid-range 100-200 seat narrow body aircraft. For smaller aircraft engines electrically powered by the hydrogen fuel cells are more economical.
Hydrogen fuel cells
Compared to hydrogen combustion hydrogen fuel cells are a more mature technology with many electric vehicles already employing such devices. Development of electric solutions in aviation, however, has been slow. In 2014 Airbus test flew the E-fan, a two seat all electric demonstrator aircraft, but the project was cancelled in 2017 in favour of a hybrid-electric aircraft. The currently available energy densities of batteries limit their application to small (that is, less than ten seat) aircraft; the largest all electric aircraft to date is the nine seater Eviation Alice, which first flew in September 2022.
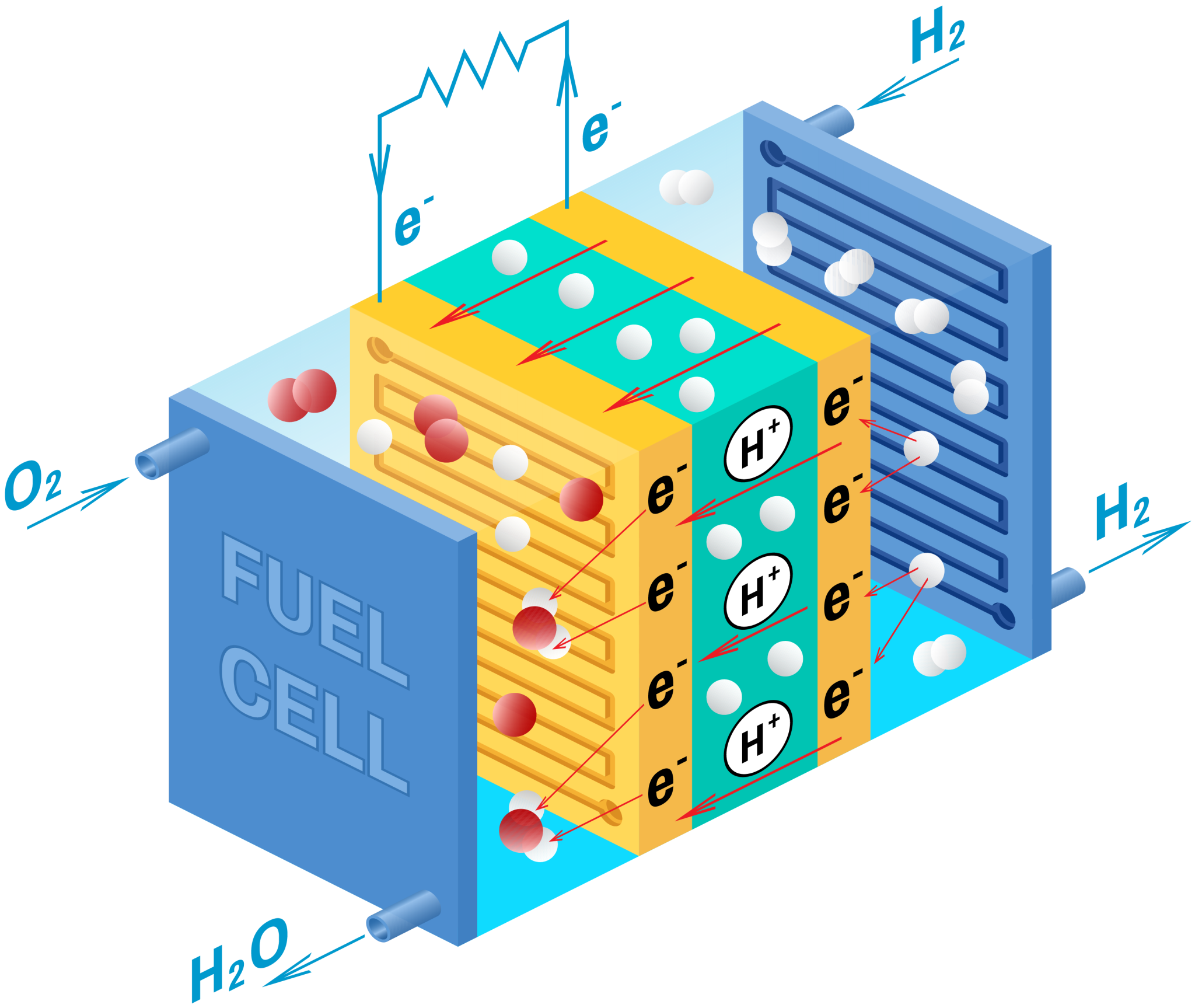
Hydrogen fuel cells have a higher energy density than batteries and therefore provides an opportunity for larger fully electric aircraft. In a hydrogen fuel cell hydrogen flows into the anode of the fuel cell, where the hydrogen reacts with a catalyst to split into protons and electrons. The protons pass through the porous electrolyte to combine with oxygen from the ambient air in the cathode to produce water. The electrons flow out of the cell to generate the electric current. Advantageously, fuel cells can continue to generate electricity as long as there is sufficient hydrogen provided, and individual fuel cells can be stacked to form larger systems capable of producing more power.
The Canadian company Universal Hydrogen hasdeveloped a conversion kit for existing aircraft, consisting of a hydrogen fuel cell powered electric propulsion unit (EPU) that replaces the existing turboprop engines and lightweight, modular hydrogen capsules accommodated in the rear of the fuselage, which can be loaded onto the aircraft using conventional pallet freight loading equipment. In March 2023 Universal Hydrogen flew a converted 50 seat De Havilland Canada DHC8-Q300, representing the largest fixed wing aircraft flown under electrical power.
Advantageously, many EPUs are electron agnostic, meaning they can be powered by any electric power source, such as conventional batteries or hydrogen fuel cells. In fact, the Universal Hydrogen De Havilland Canada DHC8-Q300 used the same EPU as the Eviation Alice, the magniX magni650, despite the maximum take-off weight (MTOW) of the Universal Hydrogen aircraft being over double that of the Eviation Alice.
Aircraft design considerations
As well as requiring a fuel tank volume four times that of kerosene, hydrogen is also only a liquid at atmospheric pressure below -253°C, so would need to be stored in large low temperature and/or pressurised tanks, adding significant weight. For both hydrogen combustion and hydrogen fuel cells, cryogenic fluid pumps and fuel lines would also be required to transport the hydrogen to the gas turbines and the fuel cells, respectively. There are additional thermal management challenges with hydrogen fuel cells, since a large amount of heat is generated by the hydrogen-oxygen chemical reaction. Universal Hydrogen filed a patent application related to supplying an amount of cooling air to the fuel stacks in anticipation of a predicted electrical demand, since the amount of heat generated by the fuel cell will not be constant during a flight cycle.
There are, however, design advantages to needing to accommodate liquid hydrogen storage. Current wing design principles are anchored around storing as much as 90% of the aircraft’s fuel in tanks in the wing. The increased tank volume and cooling requirements for liquid hydrogen means it is easier to locate the fuel tanks in the rear of the fuselage, resulting in a “dry” wing that can be optimised for wing bending moment and aeroelastic purposes. The kinematic mechanisms for the high lift devices can also be locating within the wing structure, resulting in a cleaner, more aerodynamic wing configuration.
Hydrogen storage becomes more weight and volume efficient as the tank diameter increases, so shorter aircraft with wider fuselages could be developed, potentially with variable fuselage sections to encourage laminar flow around the fuselage.
More radical new designs could be made more feasible with liquid hydrogen fuel tanks, such as blended wing bodies (BWB), where the fuselage and wing structures are smoothly blended together. In September 2024 easyJet announced that it had formed a partnership with US startup JetZero to develop future BWB aircraft which are agnostic to fuel type. JetZero has numerous patent applications directed to various aspects of the BWB design.
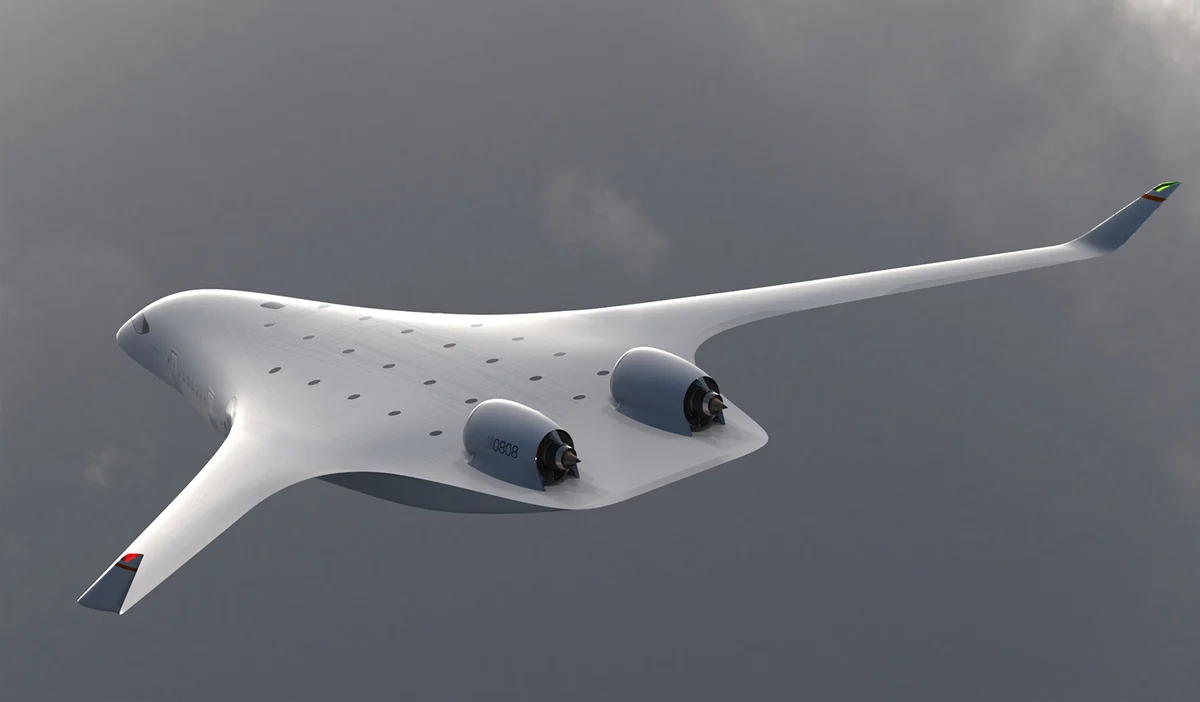
The JetZero Z4 Jet Liner blended wing body concept (source: dycip.com/jetzero-news).
One of the biggest barriers to the use of a BWB for passenger aircraft is still, however, that of passenger perception. Depending on the configuration BWBs may be windowless or have a larger number of seats per row, thereby leaving some passengers further from a window than on conventional wide body aircraft. The regulations around passenger evacuations would also be more challenging to meet. In February 2025 Cranfield University, in conjunction with the University of Greenwich, will be running a series of evacuation trials on a large BWB cabin mock-up to study have people behave when exiting such an aircraft configuration.
Green hydrogen
Although the use of hydrogen to power aircraft, either by combustion or through fuel cells, does not produce any carbon dioxide, hydrogen production is not necessary carbon natural. Currently, hydrogen is produced primarily from burning coal or natural gas, with low-carbon source hydrogen, such as from water using renewable energy, only accounting for around 0.1% of current hydrogen supplies. Further, if all planned green hydrogen projects were built they would still only account for 10% of hydrogen production by 2030.
Based on the Fly Net Zero 2050 roadmap, aviation demand for hydrogen by 2050 could represent 8-15% of future hydrogen production. Although global hydrogen demand was forecast to increase sevenfold in the same timescale this did not account for direct use of hydrogen in aircraft propulsion, so the global market for hydrogen production may be further augmented in the event of strong aviation uptake. Large-scale, clean hydrogen production therefore presents an enormous challenge.
Although scaling SAF production and use remains a key challenge in aviation for the remainder of this decade, research and investment into hydrogen-based solutions is also of high importance to ensure such hydrogen based solutions are at a sufficient level of maturity to supplement and supersede SAF in the lead up to 2050 and beyond.
Useful links
- Y Najjar, "Hydrogen safety: The road toward green technology," Journal of Hydrogen Energy, vol. 38, pp. 10716-10728, 2013.
- Cryogenic Aircraft, Internet Archive: dycip.com/cyrogenic-aircraft-archive.
- Hydrogen, the future of combustion, Polytechnique insights, 08 July 2021: dycip.com/hydrogen-future-combustion-jul21.
- Aerospace Technology Institute, “FlyZero – Hydrogen Gas Turbines & Thrust Generation Roadmap Report”, March 2022, FZO-PPN-COM-0023.
- R Domingues and F Brójo, “Conversion of Gas Turbine Combustors to Operate with a Hydrogen-Air Mixture: Modifications and Pollutant Emission Analysis”, Clean Energy Technologies - Hydrogen and Gasification Processes. IntechOpen, Dec. 07, 2022. doi: 10.5772/intechopen.106224.
- Aerospace Technology Institute, “FlyZero – Electrical Propulsion Systems Roadmap Report”, March 2022, FZO-PPN-COM-0030.
- This is what’s keeping electric planes from taking off, MIT Technology Review, 17 August 2022: dycip.com/electric-plans-mit.
- Regional Aircraft, Universal Hydrogen: dycip.com/regional-aircraft-universalhydrogen.
- magniX Powers First Flight of World's Largest Hydrogen Fuel Cell Airplane, Magnix, 02 March 2023: dycip.com/magnix-hydrogen-fuel-plane.
- Aerospace Technology Institute, “FlyZero – Zero-Carbon Emission Aircraft Concepts”, March 2022, FZO-AIN-REP-0007.
- R Wittmann, “Passenger Acceptance of BWB Configurations”, 24th International Congress of the Aeronautical Sciences, 29 August-03 September 2004.
- Help shape the future of aviation safety by taking part in our 2025 aircraft evacuation trials, Cranfield University, 04 October 2024: dycip.com/aviation-safety-cranfielduni.
- Waypoint 2050, Aviation Benefits Beyond Borders: dycip.com/waypoint-2050.
- A Battersby, "Green hydrogen's share of global H2 market could jump to 10% by 2030: Fitch Solutions”, Upstream Online, 24 May 2021: dycip.com/green-hydrogen-upstreamonline.
- CO2 Emissions in 2022, IEA, March 2023: dycip.com/Iea50-co2emissions-2022.